As base metal ores become increasingly more complex, there is mounting pressure to improve concentrator productivity. Traditional mineral processing plant control relies heavily upon operator experience and overly generalised mineralogical data to represent a constantly changing, heterogeneous mineral assemblages. But, what if there was a way to tailor plant parameters, such as reagent additions, based on real time mineralogical information?
It is accepted that the pulp chemistry varies with changes in mineralogy, reagent additions and grinding environment, and that these changes have a marked effect on the flotation of sulphide minerals (Hu et al., 2009).
Chemistry control in real-time
Magotteaux has extensive experience in making pulp chemistry measurements within a plant, as well as correlating these differences with variations in mineralogy and metallurgical performance. However, the ever changing nature of the feed mineralogy means that traditional, manual pulp chemistry measurement methods are not suitable for continuous monitoring.
To satisfy the need to measure the pulp chemistry continuously and in real time, Magotteaux developed the MagoPulp that can measure the key pulp chemistry parameters (pH, Eh, dissolved oxygen, temperature and oxygen demand) from any process stream, providing a real time proxy for the mineralogy of the mineral slurry. This data, when combined with good old-fashioned metallurgical knowhow, can be used to optimise circuit performance.
With Magotteaux’s metallurgical experience, MagoPulp can provide dynamic optimised set points in either direct control or recommendation mode. These optimisations can lead to minimising reagent usage whilst maximising recoveries.
- Real time proxy for mineralogy
- Increase recovery
- Improved plant stability
- Reduction in reagent use
- Direct control or recommendation modes
- Self-retraining algorithms tailored to your plant and mineralogy
Reference: Hu Y, Sun W & Wang D (2009), Electrochemistry of Flotation of Sulphide Minerals, Tsinghua University Press, Beijing.
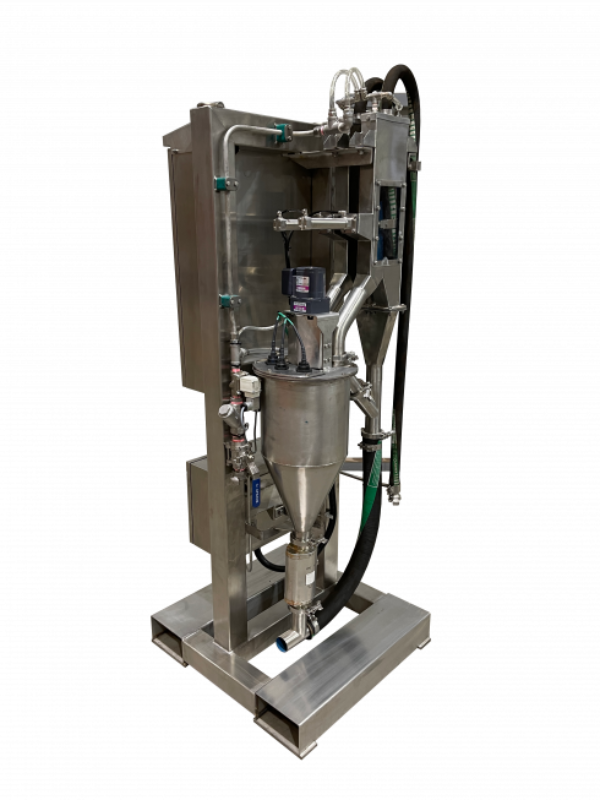